Image: Platform lift nestled within the bells (Stannah)
UK designed and manufactured lifts take pride of place in the Elizabeth Tower restoration project
By Dave Saunders, Head of Major Project Division at Stannah Lifts and John Newbold, Director at SVM Associates
For many decades, the Elizabeth Tower, the world-renown historic landmark adjacent to the Houses of Parliament in Westminster, has been displaying signs of age and exposure to pollution.
While the clock tower is often affectionately referred to as ‘Big Ben’, this is actually the nickname of the Great Bell located atop the Elizabeth Tower. The neo-gothic tower was officially unveiled during Queen Victoria’s reign in 1859. It was declared a UNESCO Heritage Site in 1987 and named Elizabeth Tower in 2012 to mark the Diamond Jubilee of Queen Elizabeth II.
Throughout the clock tower’s 162 years of existence, it has been subjected to weathering from the elements, heavy pollution, and Second World War bomb damage. Although there have been several projects undertaken to clean and refurbish the tower in the past, 2017 marked the beginning of the first complete restoration of the tower from top to bottom.
Sir Robert McAlpine Special Projects (SRM), appointed main contractor to the restoration of the iconic building, had to repair the building’s external fabric, renovate the clock, improve internal areas, add energy-efficient lighting, and oversee the installation of two lifts.
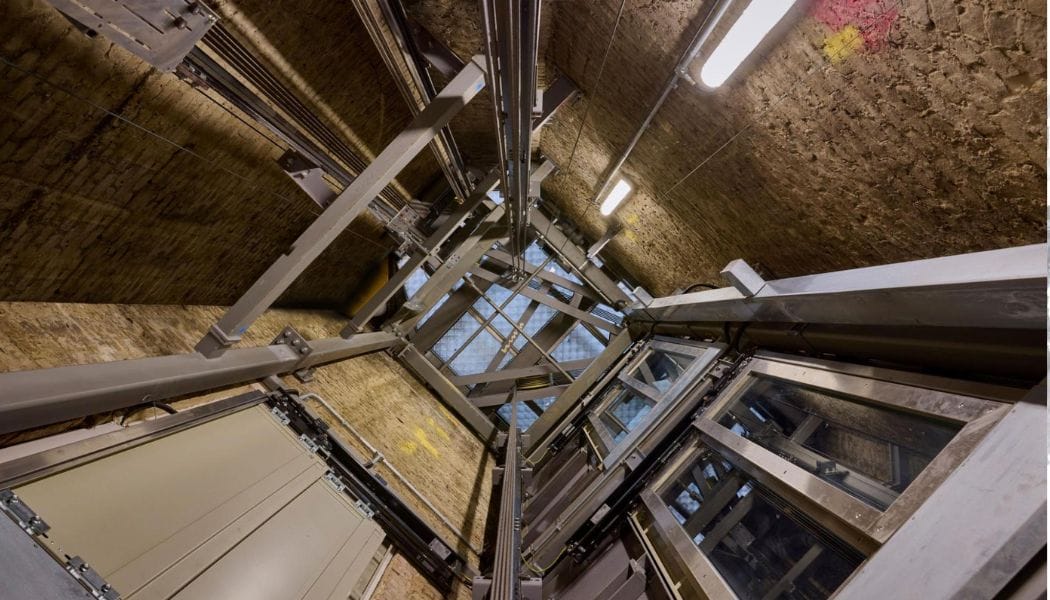
Finding space for a lift
Building a lift within a Grade 1 listed building is no simple task. Modernisations must be as inconspicuous as possible, and the addition of new building materials should under no circumstances damage the existing historic fabric of the building.
Prior to 2017, the only way to reach the top of the tower was by walking up a narrow spiral stone staircase. The 334 steps have posed a daunting deterrent for clock keepers, and the lack of lift access meant that it was extremely challenging for maintenance teams to carry equipment and parts up to the belfry.
There was an existing ventilation shaft measuring just 4.9m by 2.4m, running all the way from the base of the tower to the belfry at the very top. The challenge was to design a lift that would fit into this extremely narrow ventilation shaft, which had not been accessed since the tower’s original construction in Victorian times.
Not only did the teams have to contend with very restricted space and limiting any intrusion into the fabric of the building, but the whole tower has a slight lean of 0.23 degrees to the north-west. This means that at the top of the tower it is out of alignment by 0.22m, a crucial consideration for the design team who have had to work with millimetre clearances.
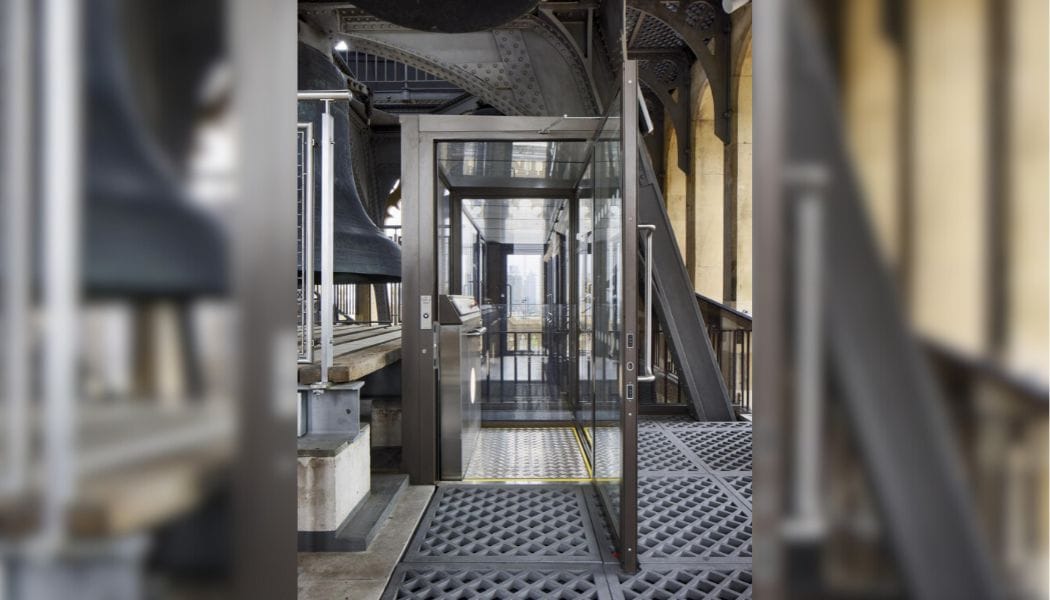
Collaboration and detailed planning
The complex and precise engineering of the lift project required close collaboration between Stannah as the lift suppliers and an independent lift consulting engineering firm, SVM Associates (SVMA). Established in 2004, SVMA design, manage, problem-solve and quality check all aspects of a lift or escalators life with clients in all sectors across the UK including high rise, commercial, healthcare, transport, education and government. SVMA has overseen lifts on behalf of Parliament’s Strategic Estates since 2013.
SVMA is employed by mechanical design engineers SI Sealy, which in turn is employed by Lendlease as the construction management company. SVMA’s role in the Elizabeth Tower lift project included lift and platform design, technical tender evaluation, involvement with design development and technical quality control.
With a legacy nearly as long as Elizabeth Tower, Stannah was founded on the banks of the Thames in London in 1867, not far downstream from Westminster. Today Stannah continues to be a family run and owned business supplying a wide range of commercial and domestic lifting products. Due to the site complexity this was a task for Major Projects – our specialist division who work on technically complex or long-period construction projects, typically in heritage sites or infrastructure, such as our extensive work for Network Rail. The Stannah Major Projects Division’s role in the Elizabeth Tower Lift Project included detailed manufacturing design of the lift and platform, installation, commissioning, and lift warranty maintenance.
Two custom built solutions
Within the 11.7m2 ventilation shaft space, a bespoke energy efficient, gearless, traction drive passenger lift was built. The lift is contained within its own structural skeleton to minimise any penetrations to the historic fabric of the building. The engineering interface between the new lift equipment and the existing historic features of the ventilation shaft, such as the original Victorian tie-rods, has been designed and installed with millimetre tolerance.
The physical constraints of the tower mean that the main lift stops two floors below the Belfry. From here, along a narrow corridor, neatly tucked into incredibly limited space, a smaller 500kg hydraulic lift platform that services the final 4295mm, between the last two floors and giving lift access to the Belfry. Due to the belfry environment the lift has been built to an external specification with 316 grade stainless steel and hot-dipped galvanized steel, chequer plate floor and IP54 rated buttons.
With a top speed of 1.5 meters per second, the main lift travels 57 meters from the ground to the eleventh floor. The lift car has strengthened, hard wearing walls and floors to ensure the lift can be used for maintenance goods as well as passengers.
The horizontal ride quality of the lift meets or surpasses the British Council for Offices Specification Guide’s requirements for passenger lifts which is testament to the lift’s precise manufacture, alignment and accurate installation and, in particular, the guide rails. Furthermore, the lift drive machinery is located away from the top of the shaft so as not to disrupt the BBC’s live recording of Big Ben’s chimes.
The Elizabeth Tower 13-person passenger lift also has a multitude of advanced energy efficient features. For instance, the regenerative drive acts as a generator whenever gravity assists the lift, thereby returning power back to the mains. The mass of the counterweight is optimised to match the likely load in the lift car, thereby saving energy, and when it is idle, the lift also turns off its non-essential power loads.
Pulleys for the ropes are made from polymer, rather than steel, so they are lighter and have less inertia, making them easier to spin – and thus are more energy efficient. Lastly, the lift is driven directly by a motor without a traditional gearbox, thereby reducing power losses from mechanical inefficiency.
Additionally, the lift incorporates all of the accessibility features required of new lifts, including controls, dimensions and enhanced audio-visual passenger information. Dual power supplies to the lift enable passengers to vacate safely if required, even if the mains power is cut off.
As for maintenance, the lift’s machinery is housed in a conventional motor room, thereby enabling maintenance personnel to access the machine and control equipment readily and safely. The lift also features advanced technology that ensures maintenance downtime is kept to a minimum. The mechanical systems such as the machine, pulleys and compensation system are virtually maintenance free. Individual rope tension is monitored by electronic transducers. Service engineers are notified when rope adjustment is required, thereby prolonging rope life. The control system is also equipped to regularly report its status and performance to a remote monitoring system.
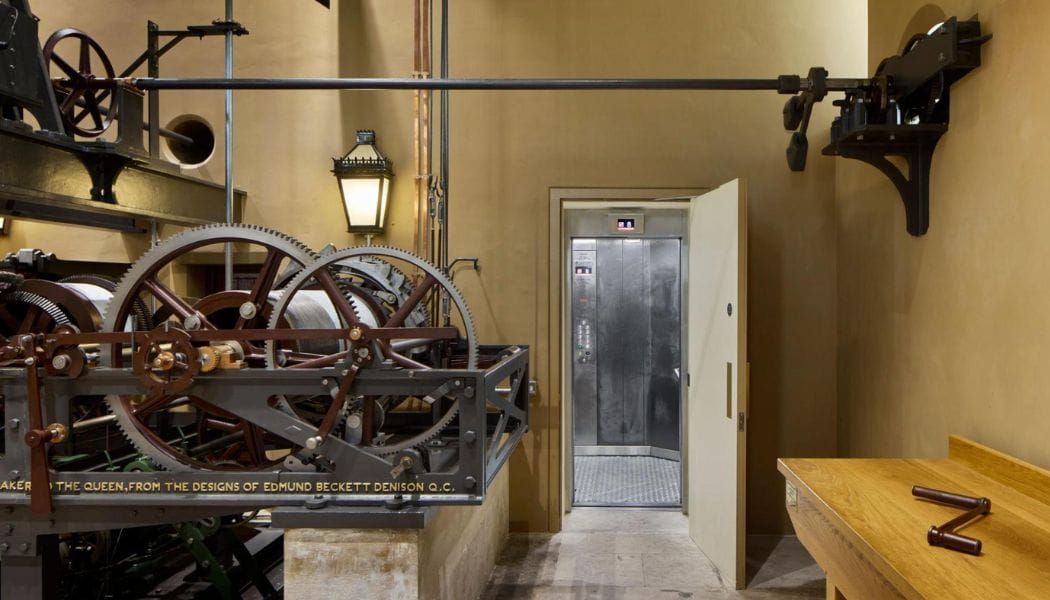
Designed safe for improved accessibility
The result of this incredibly complex and challenging project is energy efficient and precisely engineered lift systems that will make the work of the clock engineers significantly easier and could one day save lives in a medical emergency – all while preserving the historic environment of the clock tower. The designers, installers and construction teams, all of which are UK based, have inclusive and sustainable employment practises which have given a range of skilled workers a chance to work on returning a British cultural icon and symbol of democracy to its former glory.
Despite the many overriding constraints of building lifts within the 160 year old iconic structure, everything possible has been done to provide the best level of step-free maintenance access from the ground floor to the top of the tower.
“The installation of the lifts in the Elizabeth Tower restoration project has been a true feat of precision engineering and ingenuity,” said Nick Sturge, Project Manager, Sir Robert McAlpine Special Projects. “This project was enhanced by the diversity of skills and trades that made it possible and had a clear focus on sustainability, championing the use of energy efficient technologies.”
“The passenger lift is an essential modernisation component of the overall restoration project,” said John Newbold, Director at SVM Associates. “These UK designed and made lifts will ensure improved access for maintenance crew for many years to come, bringing a safe and much needed alternative to the 334 steps, especially in the event of a medical emergency.”
“This was an exceptional engineering project, made all the more challenging by site restrictions due to the COVID pandemic and stringent security requirements,” said Dave Saunders, Head of Major Project Division at Stannah Lifts. “In addition, the high profile of the Elizabeth Tower means that the eyes of the world were on us to deliver this project on time and on budget. At Stannah, we are always true to our word – we go the extra mile to deliver something we can be proud of for years to come.”
Find out more at www.stannahlifts.co.uk